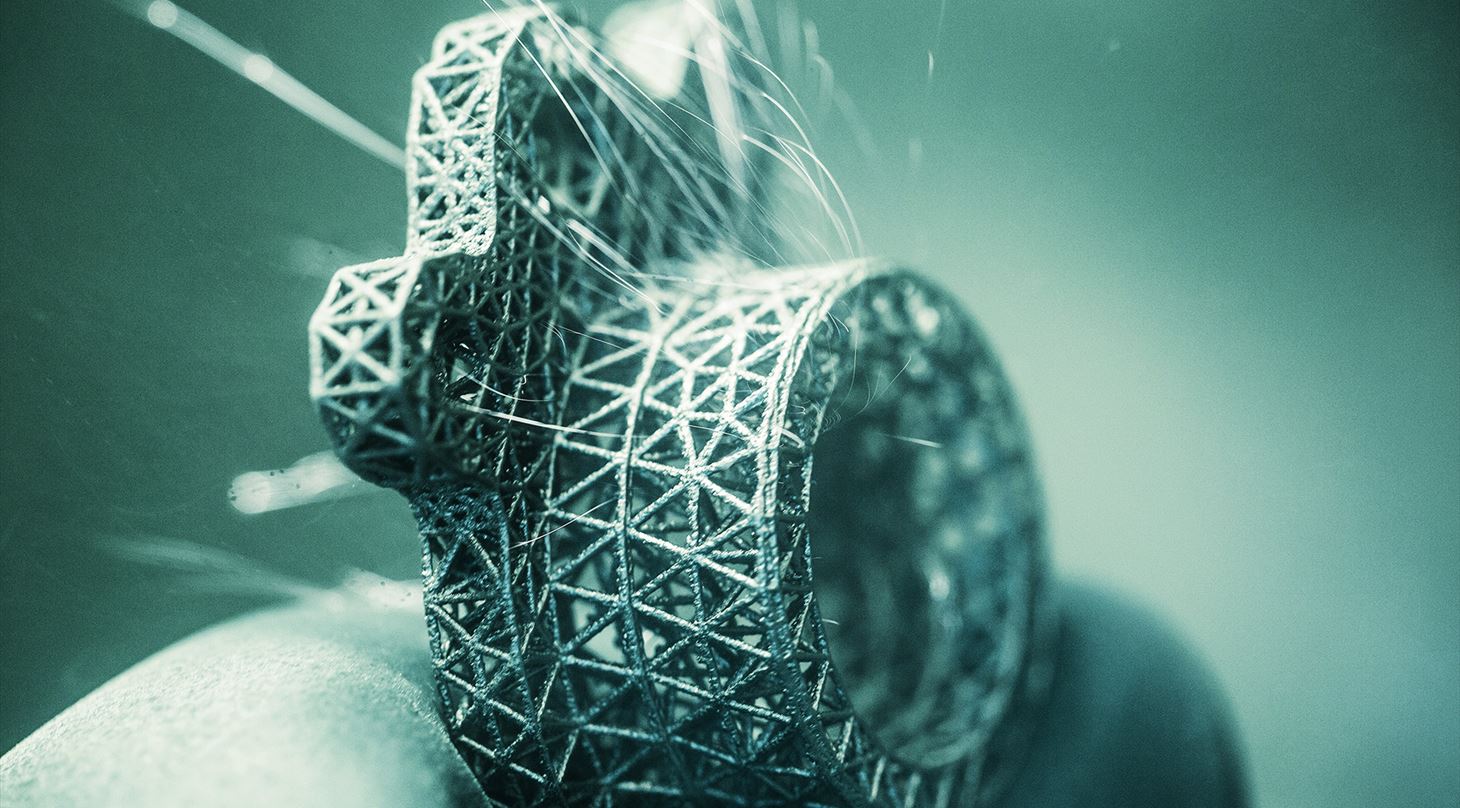
3D-print skaber øget værdi for Danfoss
Danfoss er en global aktør inden for teknologiudvikling, og tilbage i 2016 startede virksomheden på en digitaliseringsrejse. Additive manufacturing – eller 3D-print – spiller en afgørende rolle på den rejse, og det har skabt et behov for eksterne produktionsfaciliteter såvel som yderligere viden og uddannelse inden for additive manufacturing. Alt det får Danfoss i AM-LINE 4.0.
Danfoss udvikler teknologier, der gør verden i stand til få mere ud af mindre, og her spiller produktion af mekaniske komponenter en central rolle i forretningen. For en række af disse komponenter vil 3D-print kunne fungere som supplement til – og i nogle tilfælde erstatning for – mere veludviklede fremstillingsteknologier. I den forbindelse har Danfoss taget en strategisk beslutning om at arbejde med 3D-print som en del af deres digitaliseringsstrategi, og de har afsat betydelige midler til det for at sikre deres konkurrenceevne på området.
- For Danfoss er 3D-print et fornuftigt valg af flere årsager. For det første betyder designfriheden, at der er mulighed for at få bedre ydelse ind i produkterne – fx varmevekslerne - og her befinder Danfoss sig på et marked, hvor det gælder om at være mest konkurrencedygtig, når det kommer til ydelse vs. pris. For det andet er der flere tilfælde, hvor emnerne skal produceres i mindre styktal, og her giver 3D-print bedre mening end at fremstille dyrt værktøj til emnerne, lyder det Jeppe Skinnerup Byskov, leder for Industriel 3D-print på Teknologisk Institut
Danfoss har valgt at inddele 3D-print i tre kategorier: Prototyper, værktøjsfremstilling og fremstilling af slutkomponenter. Set i en kortere historisk kontekst af 3D-print er de to første kategorier - prototyper og værktøjsfremstilling – mere veludviklede, og her har Danfoss selv investeret i 3D-printere og den øvrige fornødne hardware til at håndtere fremstillingen på virksomhedens fabrik i Nordborg. Desuden er et kompetencecenter for 3D-print undervejs i USA, hvor videns-ressourcerne skal samles, mens printopgaverne lægges ud til underleverandører, og der er planer om at etablere et lignende setup i Asien.
- Hos Danfoss har vi mere end en million komponenter, og en lang række af disse komponenter er egnede til 3D-print – og til at udnytte den øgede værdi, som teknologien giver. Derfor har vi et stort fokus på, at en række af vores designs skal udvikles med henblik på 3D-print, siger Werner Stapela, Global Head of Additive Design & Manufacturing hos Danfoss.
I videoen herunder, fortæller Werner Stapela om Danfoss' arbejde med 3D-print
Tankegangen bag 3D-print skal ud i organisationen
Hos Danfoss har man fra starten haft en meget struktureret tilgang til 3D-print, og ud over en globalt ansvarlig for Additive Design & Manufacturing er der ansat 3D-print ansvarlige i hver af forretningsdivisionerne. Ude i de enkelte grupper i virksomheden er der udpeget ’champions’, som er go-to personer inden for 3D-print, og for at implementere teknologien i virksomheden såvel som i medarbejdernes mindset, at der endvidere blevet installeret små FDM-printere ude i afdelingerne. På den måde har folk mulighed for at eksperimentere med teknologien og lave små opgaver, og der har ligeledes været interne konkurrencer for at få medarbejderne til at bruge printerne.
For Danfoss har det været enormt vigtigt at komme i gang med selve tankegangen omkring 3D-print, dvs. at lære folk at designe til 3D-print og at tænke teknologien ind i forretningen, og så handler det ikke så meget om de specifikke teknologier og materialer endnu. Godt nok har Danfoss indkøbt de 3D-print maskiner, som de specifikt havde behov for, men det har betydet mere at få medarbejderne til at tænke i 3D-print og at få dem opkvalificeret på området – både gennem interne forløb og i samarbejde med eksterne partnere.
Eksterne samarbejdspartnere til metalprint
I forhold til produktion af slutkomponenter forventer Danfoss, at størstedelen af komponenterne kommer til at være i metal, så lige nu er der stort fokus på at træne og uddanne ingeniørerne og designerne, så de kan udvikle og designe produkterne med henblik på produktionsprocesserne inden for 3D-print i metal. Til gengæld har Danfoss ikke umiddelbart planer om selv at stå for produktionen, som både kræver specialiseret viden og betydelige investeringer i maskiner. I stedet vil Danfoss trække på eksisterende kompetencer på markedet og benytte samarbejdspartnere til selve produktionen af 3D-printede slutkomponenter. Her spiller AM-LINE 4.0-projektet, som er finansieret af projektpartnerne sammen med Innovationsfonden, en vigtig rolle i Danfoss’ strategi – både i forhold til uddannelse og produktion.
I den forbindelse er Teknologisk Institut en nøglepartner for Danfoss i Danmark, da Instituttet – som også er projektleder i AM-LINE 4.0 - råder over Danmarks eneste Center for Industriel 3D-print i metal. Danfoss vil således samarbejde med Teknologisk Institut om at identificere relevante cases, diskutere design, lave prototyper i metal og opbygge kompetencer, indtil de engang i fremtiden kan vurdere, om de skal hjemtage produktionen og selv investere i metal 3D-printere, eller om de skal forsætte med eksterne samarbejdspartnere – og det er langt fra sikkert, at det giver mening selv at løfte opgaven.
Men lige nu arbejder Danfoss tæt sammen med Teknologisk Institut gennem AM-LINE 4.0, og her er fokus på, hvordan Danfoss udvælger de rigtige emner til 3D-print, hvordan business casen sættes op, og hvordan emnerne optimeres, så Danfoss får mest mulig værdi for pengene og mest værdi ind i produkterne. På nogle af emnerne printer Teknologisk Institut prototyper og pilotproduktion, og herefter går produktionen i udbud med henblik på at sikre den bedst mulige produktionsøkonomi. Som en succesfuld global aktør er Danfoss nemlig nødt til at have fokus på omkostningerne, og det gennemsyrer hele deres produktion – så når de vælger 3D-print og de specifikke metalemner, der skal printes, så er det fordi det giver mening ud fra et forretningsmæssigt synspunkt.
Hjælp til bredere optag af 3D-print i dansk industri
Danfoss står som et lysende eksempel på, hvordan man arbejder målrettet med 3D-print og udnytter teknologiens muligheder, og som partner i AM-LINE 4.0-projektet er Danfoss samtidig med til at vise vejen for andre virksomheder - store som små – der gerne vil arbejde med 3D-print nu og i fremtiden.
I AM-LINE 4.0 står Center for Industriel 3D-print på Teknologisk Institut også til rådighed med en komplet produktionsfacilitet, hvor virksomheder kan udvikle og printe produkter, som de bagefter kan implementere direkte i deres egne produktionslinjer. AM-LINE tilbyder desuden uddannelse og træning af virksomheder i 3D-printteknologien, samt rådgivning i forhold til fremtidige investeringer i 3D-print.
- For virksomheder, der er nye indenfor 3D-print, vil vi kunne tilbyde en lang række tilpassede opkvalificeringsforløb - fra kortere inspirations-workshops til længerevarende forløb med de enkelte virksomheder. For de virksomheder, som er langt fremme i brugen af 3D-print, vil vi desuden stå til rådighed og vejlede dem i fx indkøb af deres egne 3D-printere eller valg af underleverandører til at opskalere deres produktion, slutter Jeppe Skinnerup Byskov.
AM-LINE 4.0-projektet er støttet af Innovationsfonden