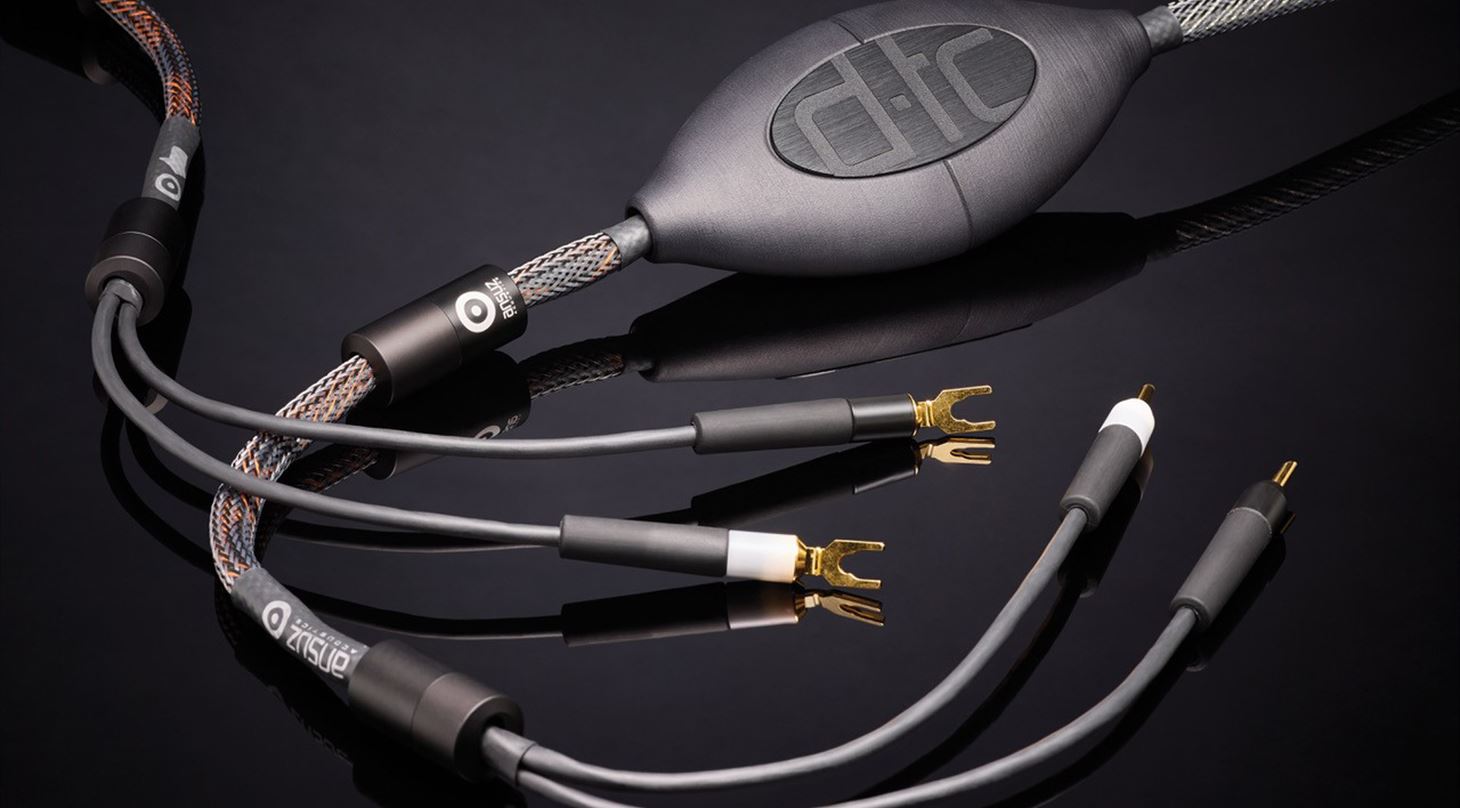
3D-print huser sublim lyd fra Ansuz Acoustics
Ansuz Acoustics er en dansk virksomhed, som udvikler og producerer kabler og tilbehør til high-end musiksystemer, og med en enorm designfrihed samt kort udviklingstid på nye produkter har 3D-print vist sig at være den helt rette løsning til de huse, hvor kablerne samles.
Ansuz Acoustics er markedsledende inden for deres snævre felt, og de sætter en ære i at forkæle deres audiofile kunder med løsninger, som får ethvert musiksystem til at yde sit maksimale. Så hvis man lige har købt en eksklusiv jubilæumspickup fra Ortofon, et NAIM audio system og et par state-of-the-art højttalere fra Aavik, er det et sæt kabler fra Ansuz Acoustics, der sætter prikken ovre i’et.
En af de teknologier, som Ansuz Acoustics har taget i brug for at nå de bedste resultater, er 3D-print, som bruges til at lave de huse, hvor kablerne samles, og hvor den elektroniske processering finder sted, så lyden i højttalerne bliver mærkbart bedre. Husene bliver 3D-printet på Teknologisk Institut, som Ansuz har arbejdet sammen med i en årrække.
- Som virksomhed har vi egentlig altid været opmærksomme på, at 3D-print fandtes. Men det, at vi kan bruge det til produktion, har noget at gøre med, at teknologien er blevet modnet over tid. Og så passer de printere, Teknologisk Institut har, som hånd i handske med de nogle af de krav, vi har til vores emner, fortæller Michael Børresen, Udviklingschef hos Ansuz Acoustics.
Til at starte med var Ansuz Acoustics kunder i Teknologisk Instituts Tribologi-center, hvor de fik lavet forskellige kosmetiske overfladebelægninger på deres produkter, og det var gennem dette samarbejde, at virksomheden for ca. fem år siden blev introduceret til 3D-print på instituttet - og de muligheder man her tilbød med teknologien.
Hi-fi-industrien er nemlig meget sæsonbestemt, og time-to-market er altafgørende. Derfor har Ansuz Acoustics brug for hurtigt at kunne udvikle komponenter til deres nye produktlanceringer og løbende vise nyheder frem på messer og lignende. Det kræver hurtige udviklingsforløb og hurtig levering, og her er 3D-print et perfekt match.
Stor designfrihed og minimal brug af værktøj
De store kabelhuse, som Teknologisk Institut 3D-printer til Ansuz Acoustics, er næsten 20 cm høje med omkreds som en halvliters drikkedunk. Tidligere blev disse huse samlet på midten, men det gjorde det sværere at sammenføre kablerne og montere elektronikken under slutproduktionen, og derfor lavede Ansuz Acoustics undervejs en designændring, så de fleste huse i dag bliver samlet på langs. Ændringen krævede ingen brug af værktøj, og den lettede produktionen for Ansuz Acoustics, og dermed er den et meget godt billede på den værdifulde designfrihed, 3D-print giver.
Når vi har valgt at bruge 3D-print i produktionen og ikke kun til designverificering, så handler det om, at vi har nogle friheder, som gør, at vi kan bygge emner, som man ikke rigtig ville kunne støbe.
- Michael Børresen, Ansuz Acoustics
Designfriheden betyder, at Ansuz Acoustics kan lave designet uden at skulle tænke på, om det fx kan lade sig gøre rent sprøjtestøbeteknisk – faktisk har man tænkt ind i designet, at man med 3D-print netop ikke får den her glatte, sprøjtestøbte overflade. Ansuz Acoustics sammenligner det selv med keramik, hvor de store huse næsten ligner en vase med drejespor fra, hvor hænderne har kørt, så man kan se naturmaterialet i det.
På baggrund af disse ønsker har Teknologisk Institut så specificeret en overflade, hvor man stadig kan se lidt af lagene fra byggeprocessen, og en sort indfarvning, som husene skal have hver gang - lige meget om det er de små eller de store modeller.
- Gennem samarbejdet med Teknologisk Institut har Ansuz Acoustics selv opbygget en større viden om, hvad man kan med 3D-print, og hvad og hvor begrænsningerne ligger, og den viden udnytter de i deres designs. Rent printteknisk kan der så være nogle ting, hvor vi optimerer processen en smule – det kan fx være noget med at tynde ud i materialet, så husene vejer mindre og dermed kan printes hurtigere, billigere og på en mere ensformig måde, lyder det fra Mads Østergaard, sektionsleder for Industriel 3D-print produktion på Teknologisk Institut.
Lad os hjælpe dig med 3D-print produktion
I udviklingsfasen benytter Ansuz Acoustics sig også meget af revisionsændringer, som er lette at lave med 3D-print. Et typisk forløb er, at Teknologisk Institut får en eller to modeller – revision A og B – som printes på samme tid. Dem får Anzuz Acoustics retur, hvorefter kabler og elektronik sattes sammen, og det hele testes. Måske kommer der så et par designændringer, hvorefter der printes nogle nye udgaver, som så igen testes. På den måde kan Ansuz Acoustics når 3-4 revisioner i løbet 1-2 uger og derefter ende med et færdigt produkt, som straks kan produceres i det ønskede styktal, og som ikke ændrer udseende i forhold til prototyperne – da alle printparametre allerede er kørt ind.
3D-print perfekt til mindre serier
Ud over at 3D-print muliggør en hurtig udviklingsfase har teknologien også den fordel, at man kan lave små serier, uden at stykprisen bliver for høj. Dette er afgørende for Ansuz Acoustics, som ikke producerer særlig store oplag af disse eksklusive kabler – og det er en vigtig grund til, at man vælger at 3D-printe kabelhusene. Således printer Teknologisk Institut i dag omkring 50-100 huse om året til de store kabler, og 2-300 huse til de mindre og billigere højttalerkabler, hvor flere kabler kan samles i et hus.
Derudover betyder produktionen med 3D-print, at Ansuz Acoustics har en meget lav lagerbinding. Mange af ordrerne til Teknologisk Institut er fx på 20 sæt med levering to uger senere i den kvalitet, Ansuz ønsker. Så både lagerbindingen og leveringstiden har også stor betydning for valget af 3D-print som produktionsteknologi.
- Vi har relativt små seriestørrelser. Vi skal ikke bruge titusindvis af emner, vi skal måske bruge hundredvis af emner af et givent design hvert år, og med 3D-print har vi en uendelig frihed til at have forskellige varianter, uden at vi har en ekstra omkostning til værktøj eller store lagerbindinger. Og så har 3D-print den fordel, som ingen andre teknologier har, nemlig at vi reelt kan have et færdigt emne i løbet af få dage. Den fleksibilitet er svær at undvære i vores virksomhed, fortæller Michael Børresen.
Med tiden er produktionen er kørt så meget ind, at designeren og udviklingschefen kun er i dialog med Teknologisk Institut, når der skal designes nye huse. Derudover er det indkøberen, som tager kontakt, når der skal bestilles flere emner – så kender Teknologisk Institut kvalitetskravene og har referenceemner liggende, så emnerne hurtigt kan produceres og leveres.
- I samarbejdet med Teknologisk Institut møder vi altid stor imødekommenhed og fleksibilitet samt en villighed til at prøve ting af. Det er nemt for mig som designer, fordi Teknologisk Institut ved, hvad der skal gøres, og hvordan finish skal være, når jeg sender mine tegninger ned, så træfsikkerheden er enormt god. Og så føler jeg mig ikke behandlet som en kunde, men mere som en samarbejdspartner, og det er virkelig godt, slutter Michael Børresen.