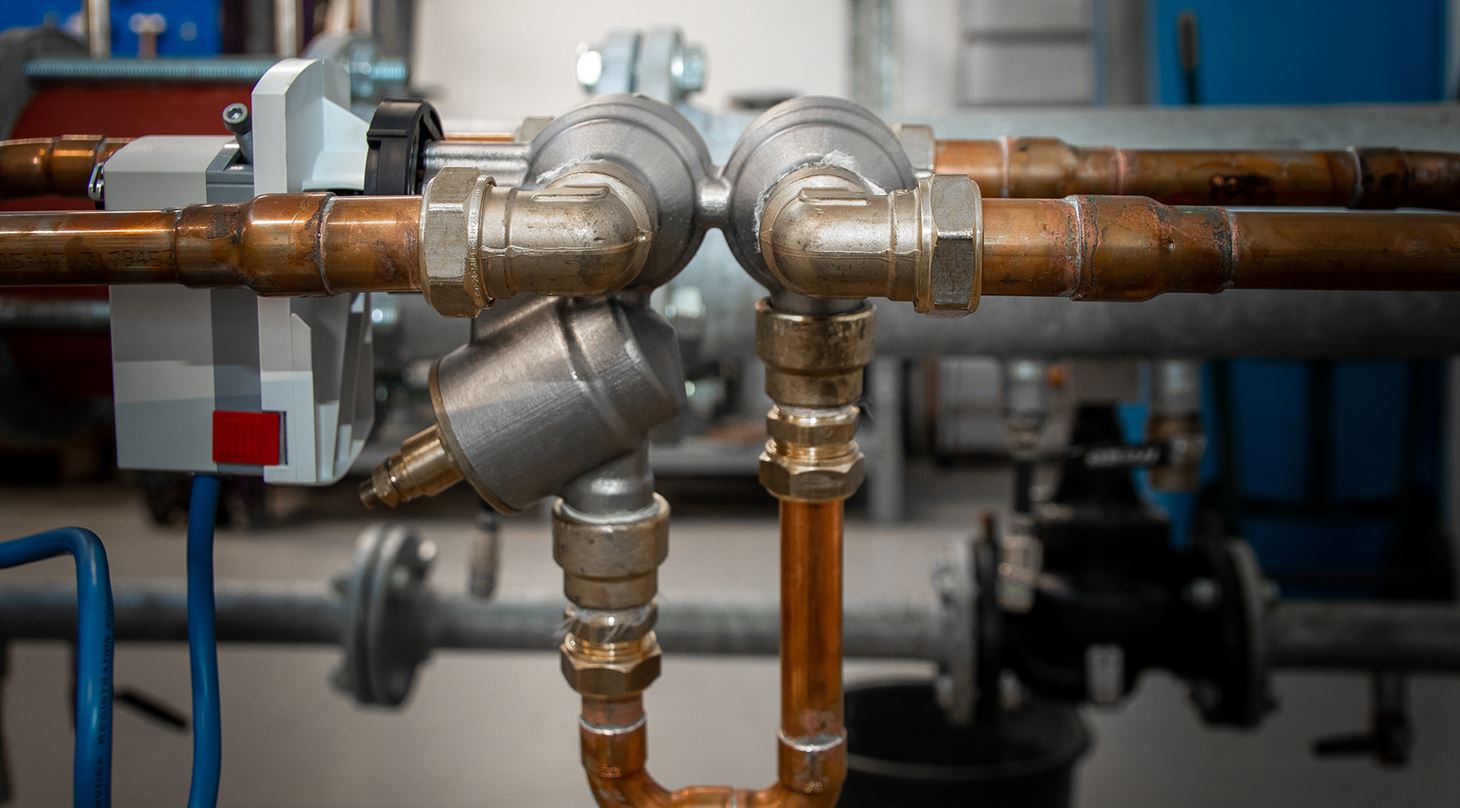
Frese udvikler speciel ventil ved brug af metal 3D-print
Den danske virksomhed Frese er en af verdens førende producenter af innovative flowstyrings- og komponentløsninger og har kunder over hele verden. I Freses udviklingsafdeling har man fokus på ventiler og fittings til HVAC-markedet, og i forbindelse med udviklingen af verdens første dynamiske seksvejs-ventil valgte Frese at benytte sig af metal 3D-print til prototyperne.
Ventilen, som Frese udviklede, er verdens første dynamiske seksvejs-ventil, som selv kan ’mærke’, om der strømmer koldt eller varmt vand igennem. Prototyperne til ventilen og det hus, den skal sidde i, blev 3D-printet i to forskellige størrelser på Teknologisk Institut, hvor Center for Industriel 3D-print tilbyder print i forskellige metaller – i dette tilfælde faldt valget på rustfrit stål.
De færdige ventiler bliver normalt lavet i messing, da det er et billigt materiale, og fordi ventilerne bliver støbt. Men Frese er begejstrede for at bruge 3D-print som prototypeværktøj, og med metal 3D-print har de haft mulighed for at udvikle prototypen med de egenskaber, den skulle have, og efterfølgende teste den under tryk. Desuden gør 3D-print det muligt at accelerere selve udviklingsforløbet, og det har betydet, at Frese hurtigt kunne udvikle og teste et nyt design.
- Det var ikke muligt for os at fremstille prototyperne, som vi plejede, og derfor stod vi overfor at skulle sætte produktionen i gang uden at have afprøvet designet. Ved at Teknologisk Institut 3D-printede prototyper af huset i rustfrit stål, havde vi mulighed for at spare en masse penge og tid ved at være sikre på det endelige design, inden vi satte støbe- varmpres værktøjerne i gang. Prototyperne blev brugt for at sikre, at vi havde den rigtige størrelse, og vi undgik at skulle lave en hel produktion af drejedele for at afklare, om dimensionerne levede op til vores funktionskrav, siger Jussi Svendsen fra Engineering Research & Development hos Frese.
I videoen herunder fortæller han mere om 3D-print udviklingen og samarbejdet med Teknologisk Institut. casen fortsætter efter videoen.
Indvendige kanaler med 3D-print
I forbindelse med designet af prototypen har Frese udnyttet en anden fordel ved 3D-print, som er muligheden for at lave rundede indvendige kanaler.
Oprindeligt var tanken, at kanalen bare skulle bores lige igennem, men i stedet fik Frese lavet prototypen med en rundet kanal inden i. På den måde har de mulighed for at teste den rundede kanal op mod en, der er lige, så de kan vurdere, hvor meget bedre den rundede er.
- Kristoffer Ryelund Nielsen, Teknologisk Institut
Skulle det vise sig, at den rundede kanal yder markant bedre, vil Frese prøve at opnå en form for runding ved at bore ind i det færdige emne flere gange. Selvom man gerne vil have funktionaliteten fra 3D-print, produceres emnet nemlig i så store styktal, at det ikke vil kunne svare sig at 3D-printe – det vil være omkring en faktor 10 dyrere end at støbe, og den merpris er svær at få kunderne til at betale. Derfor blev løsningen at bruge 3D-print som et værdifuldt værktøj i produktudviklingen og så støbe slutproduktet.
Udviklingsarbejde gav nye erfaringer
I forbindelse med udviklingsarbejdet gjorde Frese sig nogle forskellige erfaringer med, hvordan man bedst arbejder med metal 3D-print – og hvilke udfordringer man kan støde på. For eksempel var der en rids på ventilen, som Frese ikke specificeret til efterbearbejdning, og det betød, at der her var en tolerance, som ikke var så god. Læringen blev derfor, at hvis en flade er vigtig i fht. tolerancer, skal der altid lægges bearbejdningstillæg på den. Desuden ville Frese efterfølgende lave en kanal større i den 3D-printede prototype, og her erfarede man, at det var enormt svært at bore igennem, da rustfrit stål er et meget hårdt materiale – her ville den rigtige løsning derfor være at tegne kanalen lidt større på forhånd.
Lad os hjælpe dig med 3D-print produktion
Fremadrettet ser Frese et stort potentiale i at bruge metal 3D-print til lignende udviklingsforløb – men også på plastsiden er der åbnet for nye muligheder. Frese har således tidligere brugt 3D-print i resin til at producere nogle koblinger, men koblingerne sprang, fordi der var for meget tryk på, når der strømmede vand igennem. Omvendt ville 3D-print i nylon være stærkt nok til at klare trykket, men her har udfordringen tidligere været, at nylon sugede vand – men med den nye 3S-behandling fra Teknologisk Institut bliver overfladen lukket, således at nylonet ikke længere suger vand.