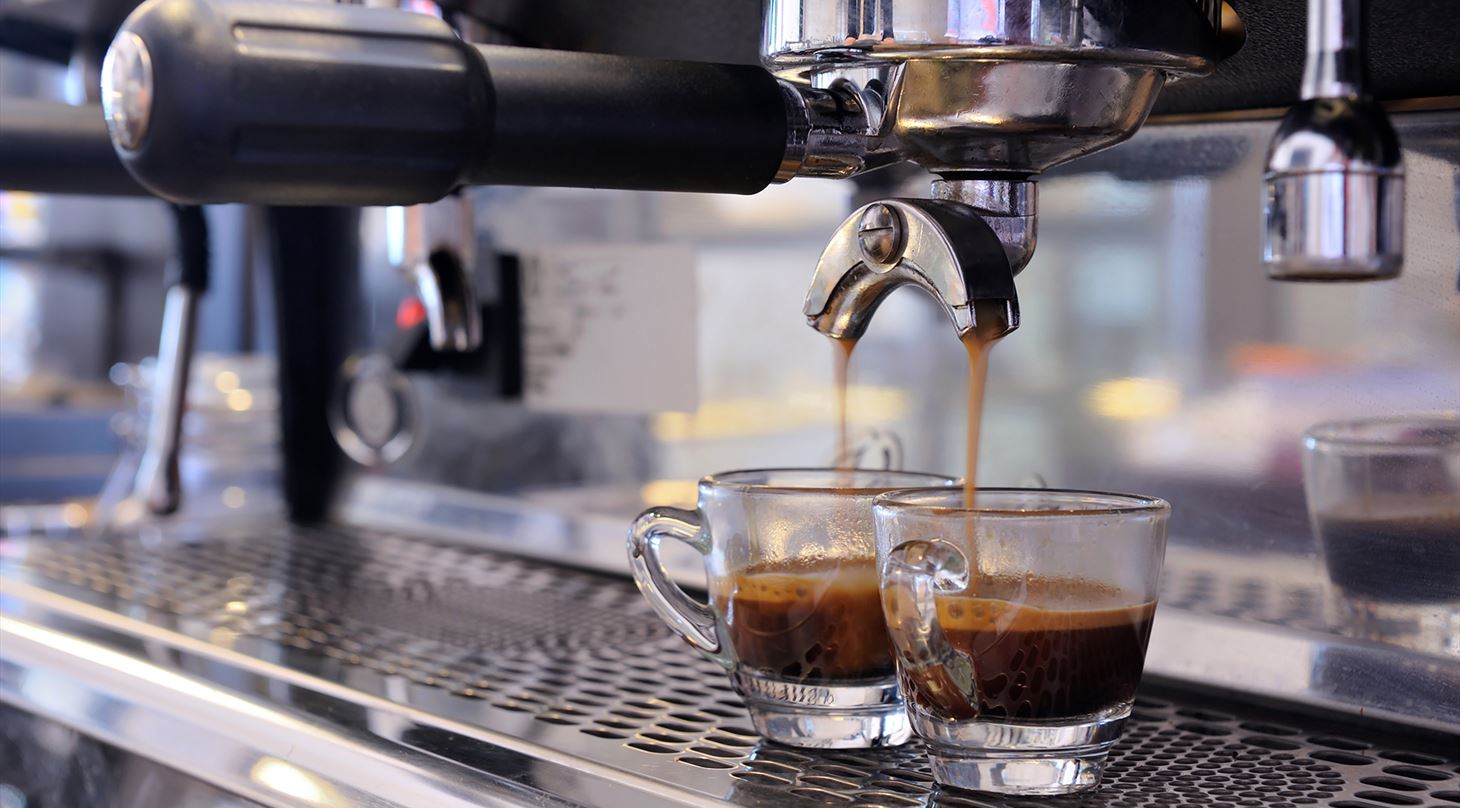
”Det er en kæmpe succes”: 3D-print vil give nyt liv til ødelagte pumper
Med metal 3D-printede reservedele er det muligt at genanvende dyre, slidte mælkepumper. Det fandt kaffeleverandøren Bentax ud af i et MADE Materiale Demonstrationsprojekt, hvor de fik hjælp af Teknologisk Institut. Teknologien reducerer spild og udgifter i produktionen og åbner også op for en række anvendelser på andre områder.
En stor bunke ubrugelige mælkepumper ligger i et hjørne og samler støv.
Måske de dyre kasserede dele fra kaffemaskiner kan genanvendes og få nyt liv frem for at smides ud?
Det spørgsmål undersøgte virksomheden Bentax, der er totalleverandør af kaffeløsninger til virksomheder og udsalgssteder, sammen med Teknologisk Institut i et MADE Materiale Demonstrationsprojekt.
Test viser, at man kan metal 3D-printe reservedele til de ødelagte pumper, så de leverer næsten som en ny pumpe. Næste skridt bliver at reservedelene og de genanvendelige pumper nu skal justeres og testes grundigt hos en virksomhed.
Nu og her er det en kæmpe succes, og vi er godt tilfredse med, hvor det ligger prismæssigt, så vi er klar til næste runde med 3D-print, og så er det en fantastisk historie for os at kunne fortælle vores kunder
- Anders Myrup, Bentax
Mælkepumper er roden til alt ondt
I forbindelse med service har Bentax oplevet en udfordring med mælkepumpen, hvor nogle dele bliver slidt hurtigt. Det er en stor udgift, da man ikke kan få løse reservedele til pumpen, og derfor er nødt til at købe en helt ny pumpe hos leverandøren. Det har betydet, at Bentax nu ligger inde med en stor bunke ubrugelige mælkepumper, som egentlig fungerer fint bortset fra to slidte dele.
- Disse mælkepumper er roden til alt ondt i en kaffemaskine, for hvis de ikke fungerer optimalt, er der mange andre dyre dele omkring pumpen, der går til. Det kræver mange udkørsler og gør, at den enkelte tekniker ikke kan håndtere lige så mange kunder, så det kræver flere ansatte, flere servicebiler etc. Så for at stoppe den onde spiral er det vigtigt, at pumpen fungerer optimalt, fortæller Anders Myrup, Teknisk Projektleder hos Bentax.
Løsningen skulle findes i et MADE Materiale Demonstrationsprojekt: Målet var at undersøge, om man kunne 3D-printe de kritiske reservedele i metal og dermed genanvende de dyre pumper i stedet for at skulle købe helt nye – og samtidig se, om man kunne få pumperne til at holde længere?
- Vi har valgt den sværeste opgave til at prøve 3D-print af, og den der giver os flest udfordringer. Hvis vi kan løse den, så kan vi løse alt. Desuden sidder vi på den ’grønne’ gren og vil gerne løse vores opgaver på en mere ansvarsfuld og bæredygtig måde. Så det ville være interessant, hvis vi i højere grad kunne digitalisere varelageret og samtidig få fremstillet komponenter lokalt i stedet for at få dem sendt fra den anden side af jorden, siger Anders Myrup.
Moderne 3D-print teknologi møder traditionelt håndværk
I projektet har Bentax helt konkret kigget på de 10 procent af mælkepumpen, som typisk bliver slidt. Det drejer sig om nogle tandhjul og et lille hus til disse, og problemet er, at tandhjulene skærer sig ind i huset over tid og laver nogle spor, som gør at pumpen ikke kan levere det ønskede resultat.
I første omgang er målet at pumpe noget liv ind i de ødelagte pumper, så vi kan genanvende dem. På sigt vil vi gerne kunne nøjes med at lave reservedelene frem for at købe nye pumper hos leverandøren, også vil vi også gerne opnå en længere holdbarhed og en lavere pris sammenlignet med en ny pumpe
- Anders Myrup, Bentax
I projektet er hele pumpen blevet scannet og opmålt på Teknologisk Institut, som har lavet en tro digital kopi. Herefter er huset blevet 3D-printet i rustfrit stål og efterbearbejdet ned til de ønskede tolerancer, som er meget fine. Tandhjulene blev også forsøgt 3D-printet, men de var ikke stærke nok, og derfor er de i stedet blevet fræset ud med traditionel CNC-fræser i et materiale, der hedder Peek.
Undervejs har der været sparring mellem Bentax og Teknologisk Institut, og det har ført til tre forskellige designudgaver, som er blevet testet. Ved udgangen af projektet er man ikke langt fra målet i forhold til at opnå det ønskede resultat fra pumpen. Det 3D-printede hus er helt på plads, men der skal stadig laves nogle helt fine justeringer på tandhjulene.
På sigt skal komponenterne overfladebehandles med kromnitrid, så overfladen ikke brydes, når tandhjulene arbejder imod den, og forventningen er, at det vil forøge holdbarheden.
Skepsis gjort til skamme
I projektet er Bentax blevet positivt overraskede over mulighederne inden for metal 3D-print.
De resultater, vi har set, er ud over al forventning, og da vi stod med de emner i hånden, var der ikke rigtig nogen, der troede på, at de var 3D-printet. Det var langt ud over, hvad vi troede var muligt, så vi havde tydeligvis ikke stor nok indsigt i teknologien
- Anders Myrup, Bentax
Anders Myrup fremhæver samtidig MADE demonstrationsprojektet som en fantastisk mulighed for at afprøve en ny teknologi og mane tvivlsspørgsmål i jorden:
- Når man er en gammel købmandsbutik, som vi er, så er man altid skeptisk over for ny teknologi og for bare at springe ud i det. Så det er jo helt fantastisk, at man kan få det afdækket og finansieret i sådan et projekt. Vi har nu haft mulighed for at verificere en teknologi, som vi ikke ellers ville være sprunget på - så var vi nok gået andre veje eller var blevet, hvor vi var. Vi havde i hvert fald ikke gjort det i den skala og med den hast, som vi gør det i nu. Så den skepsis vi havde, den blev gjort til skamme, understreger han.
”Vi stopper ikke her”
MADE Materiale Demonstrationsprojektet er nu afsluttet, men Bentax er stadig i gang med den sidste tilretning af tandhjulene. Herefter skal hele sættet i maskine, så outputtet kan verificeres, og så skal det i en kundes maskine, hvor Bentax vil overvåge det over en 15 måneders periode. Men man er allerede nu klar til at gå videre med 3D-print.
- Vi stopper ikke her, selvom projektet er slut, og vi endnu ikke har alle svarene, for projektet har vist, at 3D-print giver mening. Nu og her er det en kæmpe succes, og vi er godt tilfredse med, hvor det ligger prismæssigt, så vi er klar til næste runde med 3D-print, og så er det en fantastisk historie for os at kunne fortælle vores kunder, lyder det fra Anders Myrup.
Bentax er allerede begyndt at kortlægge andre komponenter, der kunne være egnede til 3D-print med henblik på fremtidige projekter.
- Vi ser mange flere muligheder nu, også ud over de dele, vi propper i maskinerne. Det kunne være specialdesignede værktøjer eller tilpassede holdere og kroge til arbejdsbordene i værkstedet, så vi kan optimere vores processer - og det er afledt af det her projekt, siger Anders Myrup og tilføjer afsluttende:
- Jeg tænker, at når vi skal videreudvikle vores varelager og digitalisere det yderligere, så vil det også være 3D-print, der kommer til at danne grundlaget.
Om MADE Demonstrationsprojekter
Med et MADE Demonstrationsprojekt kan en lille eller mellemstor virksomhed få op til 100.000 kroner i støtte til at løse en konkret udfordring i virksomheden eller afprøve en ny teknologi i produktionen.
Der er løbende ansøgningsfrist på demonstrationsprojekter både inden for materiale og produktion.
Næste frist for ansøgning er d. 1. december 2022
MADE Demonstrationsprojektet er muliggjort ved finansiering fra Industriens Fond.