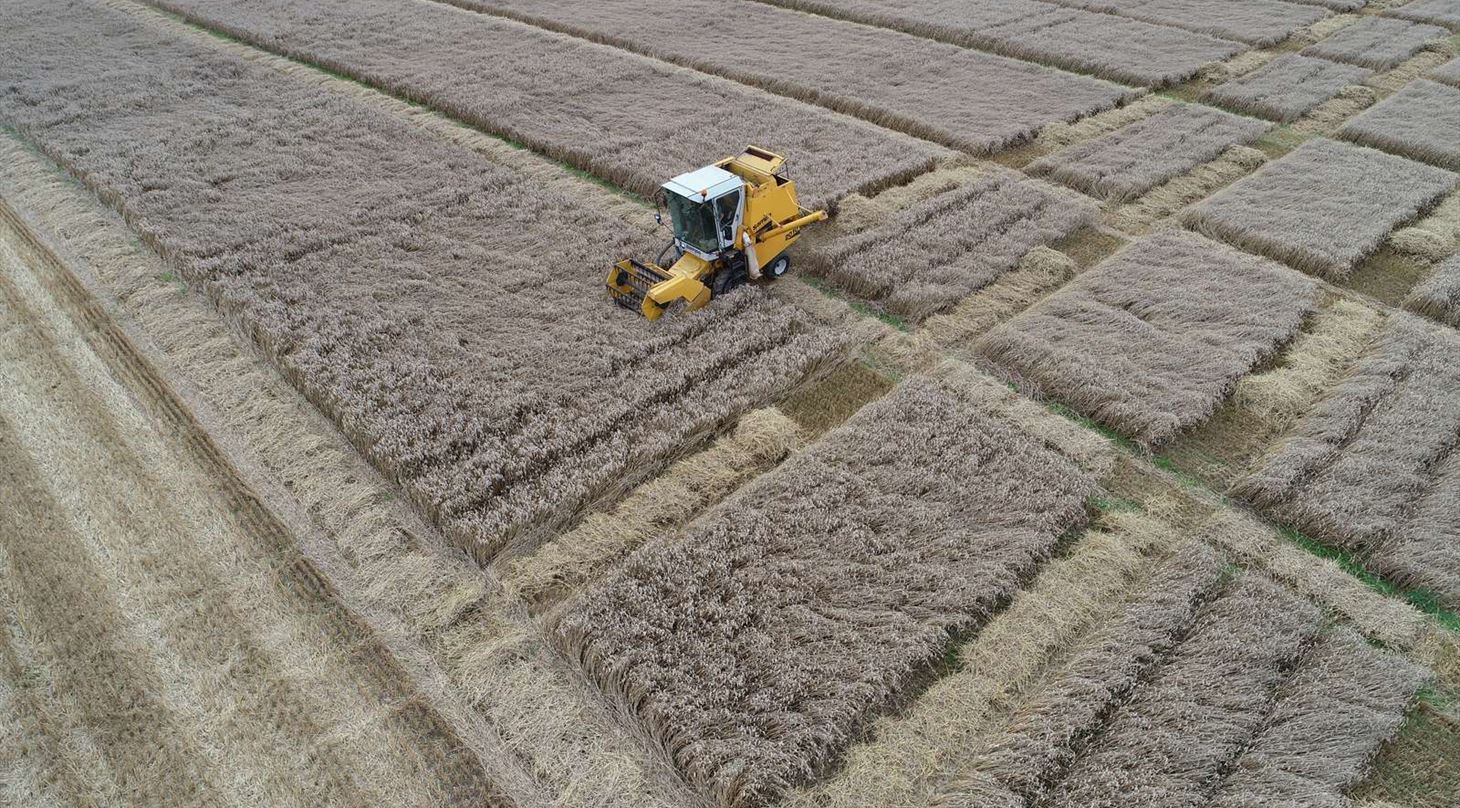
3D-print af bakker til prøveglas førte til store besparelser
Teknologisk Institut har mange specialiserede fagligheder, som hver især skaber imponerende resultater. Men når man udnytter synergierne mellem de forskellige kompetencer, kan det føre til endnu flere fordele – både internt og for kunderne. Et af de seneste eksempler var et samarbejde mellem specialisterne inden for 3D-print samt mark- og fødevareteknologi, som førte til enorme besparelser og øget fleksibilitet.
I foråret 2022 stod Teknologisk Instituts afdelinger for henholdsvis mark- og fødevareteknologi med en udfordring i forbindelse med et stort projekt, der alene det første år omhandlede udtagelse og analyse af godt 30.000 lattergas-prøver.
I den forbindelse havde man investeret i en analysemaskine med en såkaldt autosampler, så analysen af de mange prøver kunne automatiseres mest muligt – både af hensyn til tid men også for at eliminere manuelle fejl i processen mest muligt. Det sker ved, at en række prøveglas placeres i en bakke, som så sættes ind i maskinen, hvor prøverne tages.
- Autosampleren kom med to bakker, som hver havde 60 positioner til prøveglas. Det var jo åbenlyst ikke nok i forhold til vores prøvemængde, da vi skulle op på minimum 300 analyser i døgnet, fortæller Sune Petersen, konsulent på Teknologisk Institut.
Behov for tilpasning – og mere plads
Udfordringen var altså dels, at man gerne ville have flere bakker, men samtidig ville man også gerne have plads til flere prøveglas på bakken – og faktisk også nogle andre størrelser glas end dem, man havde, som så skulle arrangeres på en anden måde på bakken. MEN: Holderen, som i dag fremstilles i aluminium, er bekostelig hos producenten – så det var simpelthen for dyrt bare lige at bestille nye.
Jeg kontaktede producenten og fik en pris for 8 bakker med plads til 60 prøveglas hver, som lå over vores budget. Så kom jeg i tanke om et LinkedIn-opslag fra vores kollegaer i 3D-print, som havde printet en vanvittig flot hånd i titanium, og jeg tænkte, at vi hvis de kunne lave den, kunne de nok også lave bakker til os
- Sune Petersen, Teknologisk Institut
Ønsket var derfor at få designet en ny holder, som kunne 3D-printes i plast, da der ikke var krav om, at det skulle være aluminium – og samtidig ville man gerne reducere prisen. Derfor blev specialisterne i Industriel 3D-print kontaktet, og de lavede et design og den første prototype på blot et par uger. Efterfølgende blev designet justeret, så man endte med den helt rigtige løsning.
Lavere pris og større fleksibilitet
- Resultatet blev et design, som let kunne tilpasses til de forskellige prøveopsætninger. Den nye bakke i plast kunne 3D-printes væsentligt billigere, så det giver en kæmpe besparelse og samtidig en øget fleksibilitet, da designet er let at tilpasse, fortæller konsulent Sigurd Vigen Pedersen, som har lavet de 3D-printede bakker.
Indtil videre er der blevet printet 22 nye bakker, og det har givet en besparelse på lige knap 85 procent – og de nye bakker kan leveres inden for 10 dage, selv når der er tale om nye designs.
Takket være Teknologisk Instituts mangfoldige kompetencer har vi i dag et setup, der både design- og prismæssigt er langt overlegent sammenlignet med ’hyldevaren’ fra producenten
- Sune Petersen, Teknologisk Institut