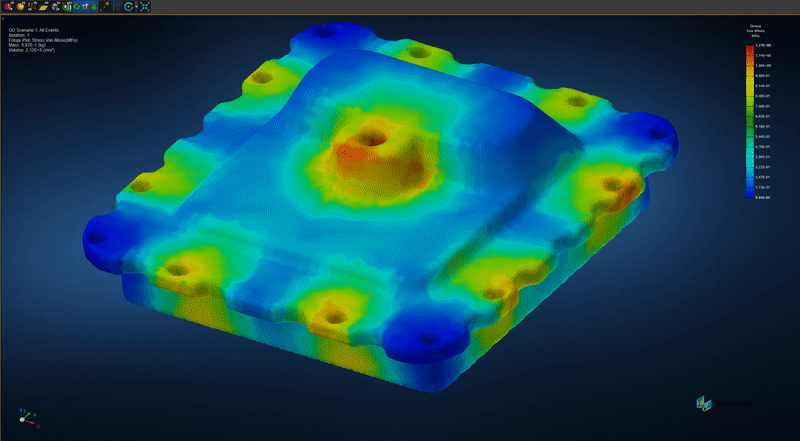
BEWI fik lavere pris, kortere leveringstid og øget effektivitet med 3D-print
BEWI producerer Flamingo® - og man har været nysgerrige omkring 3D-print. Men da man blev tilbudt et 3D-print designforløb i samarbejde med Teknologisk Institut og Dansk AM Hub, vidste man ikke, at resultaterne skulle vise sig at have et kæmpe potentiale for BEWIs fremtidige komponenter. Men med 3D-print kan man faktisk reducere både vægt, pris og leveringstid på nogle af de værktøjer, der bruges i processen - og så ser de ud til at være mere effektive.
BEWI er en plastvirksomhed, som producerer polystyren - det vi i Danmark kender som Flamingo® - i kundetilpassede løsninger. Når de komplekse geometrier i Flamingo® ikke kan produceres på traditionel vis, kræver det et støbeværktøj, der kan støbe komplekse forme og designs ud fra kundernes ønsker. Selve støbeprocessen kræver støbeforme med gode varmeledningsegenskaber, der hurtigt skal kunne nedkøles og opvarmes igen.
Derfor var BEWI interesseret i at undersøge, hvorvidt det var muligt at effektivisere cyklussen ved brug af 3D-printede støbeforme i aluminium, hvor en hurtig afkøling og opvarmning er afgørende for potentielt at øge kapaciteten med mindst muligt energiforbrug.
Det kiggede man på i et 3D-print designoptimeringsforløb sammen med Teknologisk Institut, hvor man optimerede et af værktøjerne, som indgår i støbeprocessen. Målet var at få en printet løsning, som kan bidrage med fleksibilitet.
I videoen herunder fortæller udviklingsmanager Ole Krebs fra BEWI om designforløbet og potentialet i 3D-print teknologien.
En effektiv produktion er en afgørende parameter
Et oplagt sted at tage BEWIs støbeforme under lup var i forhold til reduktion af vægt. Her er 3D-prints designfrihed blevet et afgørende element for at opnå BEWIs ønske om en mere effektiv produktion.
Missionen lykkedes til fulde. I forløbet, som var initieret af Dansk AM-Hub, optimerede man designet på værktøjet, og derved har man først og fremmest reduceret vægten med 74 procent i forhold til traditionelt værktøj, men også forbedret time-to-market ved blandt andet at have skåret 25 procent af leveringstiden.
- BEWIs nuværende støbeforme bliver fræset i aluminium og består af tre dele. De bliver efterfølgende samlet og får en vægt på 550 gram. Udfordringen med disse støbeforme er, at de er dyre at fremstille, og samtidig har de svært ved at afgive varme. Tilmed er de fræsede støbeforme også komplekse at lave, og derfor møder BEWI ofte begrænsninger, når det kommer til design, lyder det fra Morten Lisberg Jørgensen, konsulent på Teknologisk Institut.
Pluspoint på designfriheden
Undervejs i projektet var det oplagt at kigge nærmere på mulighederne for at forbedre designet med topologioptimering, hvor man får en computer til at beregne det mest ideelle design ud fra en række parametre, som man angiver på forhånd. 3D-print har som bekendt en høj designfrihed, da der ikke er de samme begrænsninger i selve fremstillingen, og i projektet fik BEWI mulighed for at samarbejde med virksomheden Hexagon, der er eksperter inden for topologioptimering – det afdækkede et enormt potentiale for BEWI.
Det giver en enorm fleksibilitet og er et potentiale, hvor vi ved at optimere værktøjet kan tilbyde mere komplekse og bedre løsninger på både kvalitet og økonomi og dermed møde de udfordringer, som vores maskinindstillinger ikke kan hjælpe os med. Desuden ser vi tegn på, at den optimerede komponent kan øge vores produktionskapacitet og sænke energiforbruget i produktionen, hvis vi implementerer den bredt – simpelthen fordi den er mere effektiv
- Ole Krebs, BEWI
Fra 6 uger til 10 arbejdsdage – og 74 % vægtreduktion
Med 3D-prints designfrihed har BEWI selv kunnet bestemme geometrien, som de ellers var begrænset af før. Støbeformene bliver printet i aluminium, som er et materiale, BEWI er vant til at arbejde med. I løbet af projektet er det lykkedes at reducere støbeformens vægt med 74% blot ved optimere designet. Komponentens vægt er gået fra 550 gram til 145 gram. Det er helt essentielt, fordi det betyder et markant mindre materialeforbrug. Derudover sparer BEWI ved brug af 3D-print også en hel del på leveringstiden på støbeformene: Leveringstiden på de fræsede støbeforme ligger på 4-6 uger, hvorimod den 3D-printede støbeform har en leveringstid på kun 10 dage.
Den reducerede leveringstid har høj værdi for BEWI. Det betyder, at de ikke behøver at stå stille med deres produktion i særlig lang tid og derved hurtigere kan komme i gang med nye projekter. Foruden designfriheden får de også mere frihed i produktionen til hurtigt at kunne afprøve nye ideer
- Morten Lisberg Jørgensen, Teknologisk Institut
Fremtiden byder forhåbentligt på mere 3D-print
En anden fordel ved de 3D-printede støbeforme er, at BEWI halverer prisen, og det skyldes blandt andet den reduceret masse. Projektet blev afsluttet med en fysisk test af de 3D-printede støbeforme for at verificere deres levetid, og testen viste positive resultater. Sammenlignet med tidligere projekter har den helt store forskel været, at BEWI i projektet har fået nogle resultater, de kan gå ud og bruge i morgen.
- Vi kan lave en løsning til kunden, der giver en større økonomisk gevinst for dem fordi vi kan friholde dem fra nogle omkostninger. Det kan fx være en hurtigere samletid og at være mere effektiv på flere områder. Og det er nok den store driver for os for at blive i et marked, der udvikler sig hastigt: At vi kan tilbyde noget ekstra og så stadig være konkurrencedygtige, lyder det afsluttende fra Ole Krebs.
Kort om DfAM-forløbet
I løbet af 2022 har Dansk AM Hub i samarbejde med partnerne Teknologisk Institut, PLM Group, Hexagon og Wikifactory haft 15 danske SMV’er gennem et nyt innovationsforløb med henblik på at styrke virksomhederne til i endnu højere grad at drage fordel af det teknologiske og forretningsmæssige potentiale inden for 3D-print. Forløbet kaldes Design for Additive Manufacturing (eller DfAM) og fokuserer på at udbrede 3D-print til små- og mellemstore virksomheder samt at yde konkret støtte og hjælp til at arbejde med teknologien gennem design. Det konkrete mål for DfAM-forløbet er at re-designe deltagernes produkter eller komponenter, hvilket muliggør, at disse f.eks. kan fremstilles med større styrke, mindre materialespild, ny og bedre funktionalitet samt on-demand.