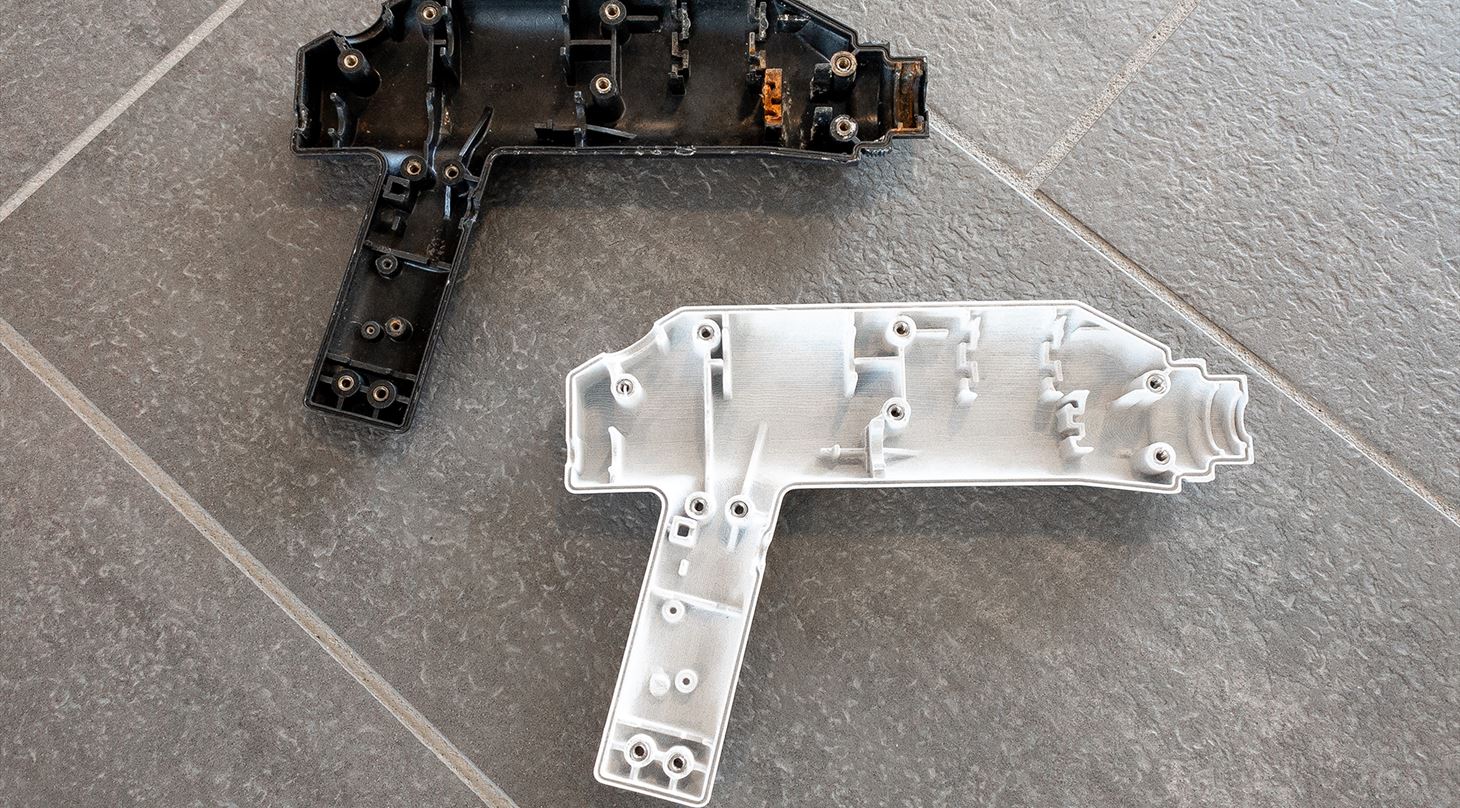
Reverse engineering af 3D-printet ‘hangris-pistol’ til DMRI og Danish Crown
DMRI - Danish Meat Research Institute fik en opgave om at gen-producere en pistol til udtagning af vævsprøver på hangrise, da pistolen var ved at udgå af lager hos Danish Crown. Hverken tegninger eller sprøjtestøbeværktøj eksisterede dog længere, og derfor blev løsningen at lave ‘reverse engineering’ ved hjælp af CT-scanning og 3D-print.
Danish Crown fik for 20-25 år siden DMRI - Danish Meat Research Institute til at udvikle en pistol til udtagning af vævsprøver på deres hangrise, så de kunne teste skatol-niveauet. Pistolen blev i sin tid masseproduceret ved hjælp af sprøjtestøbning. Der blev således lavet en sprøjtestøbeform for selve pistolen, og Danish Crown købte alle de færdige pistoler.
Fast forward til 2019, hvor Danish Crown nu er løbet tør for pistoler og derfor henvender sig til DMRI for at købe nogle flere. Udfordringen er nu, at den originale sprøjtestøbeform er skrottet efter bare at have stået og fyldt i mange år, og ingen ved, hvem der havde lavet den, eller hvor pistolerne blev produceret. Så hvordan optimerer og gen-producerer man et eksisterende produkt uden at have noget der ligner en CAD-fil?
Reverse engineering med CT-scanning og 3D-print
Heldigvis var den mand, som lagde den elektroniske indmad ind i de oprindelige pistolskaller, stadig ansat hos DMRI, og han havde en af de originale pistoler tilbage.
Den pistol, jeg havde liggende, havde ikke været i brug, og derfor var den næsten i perfekt stand - i modsætning til dem vi kunne få fra Danish Crown, som havde været i brug i mange år og efterhånden var holdt sammen af gaffatape.
- Kristen Pedersen, Konsulent hos DMRI
Med et sæt pistolskaller i hånden var det nærliggende at få dem 3D-scannet hos Teknologisk Instituts afdeling for Måling og Kvalitet, så skallerne kunne omsættes til en modellerbar 3D-tegning, som DMRI kunne arbejde videre med.
Lad os hjælpe dig med 3D-print produktion
- Med den feedback, vi havde fået fra Danish Crown samt Kristen Pedersens viden, kunne vi optimere den nye 3D-model ved at forstærke nogle punkter i pistolskallerne, så de blev mere holdbare end før. Herefter var det oplagt af få Center for Industriel 3D-print til at 3D-printe de nye skaller, fortæller Simon Nybo Johansen, der som konsulent hos DMRI har håndteret opgaven med nye pistoler.
Hurtig udvikling og produktion til lavere pris
Med designfilerne, som nu var optimeret til 3D-print, var det hurtigt at printe skallerne til de nye pistoler i nylon - og skulle der blive behov for flere pistoler i fremtiden, kan de hurtigt 3D-printes igen, nu hvor designfilerne er lavet.
De nye pistoler har ikke krævet ny elektronik, og hele forløbet har ikke taget mere end en måneds tid, inklusive scanning og opmåling, produktion af designfil, designoptimering samt færdige 3D-print af emner til levering. Det er nogenlunde samme tid, som det ville tage at lave et nyt støbeværktøj - og herefter ville produktionen skulle tilpasses. Så denne løsning har både været hurtigere og på grund af det lave styktal også væsentligt billigere end sprøjtestøbning.
One-stop-shop på Teknologisk Institut
Hos DMRI har man været meget begejstret for forløbet og hele måden at løse problemet på med CT-scanning og 3D-print, da det er en effektiv og hurtig metode til både udvikling og produktion - og Danish Crown har ligeledes været tilfredse med resultatet. Derfor ser man hos DMRI et potentiale i bruge disse teknologier i fremtiden, og i den forbindelse er det en fordel at have en lang række specialkompetencer samlet under ét tag på Teknologisk Institut. En af de helt store fordele ved samarbejdet med Center for Industriel 3D-print har fx været, at de har mulighed for at 3D-printe i materialer, der er godkendt til fødevarekontakt.
- Jeg tror ikke, at kunden ved, hvilken tur vi har været igennem for at skaffe produktet til dem, men hos DMRI er vi rigtig glade for at have alle de kompetencer til rådighed på Teknologisk Institut, som vi nu engang har. Hvis ikke vi havde haft disse kompetencer, havde vi ikke kunne fremskaffe et produkt til kunden, slutter Simon Nybo Johansen.
I første omgang er der er leveret seks hangris-pistoler, men forventningen er, at der skal produceres yderligere 10 stk., som vil blive printet i metaldetekterbart nylon, så de er mindre modtagelige over for smuds.